Pop Up Villages Could be the Quick Solution to High Growth Areas
Written By: James Aiken
Email | LinkedIn
Social Housing through Temporary Villages
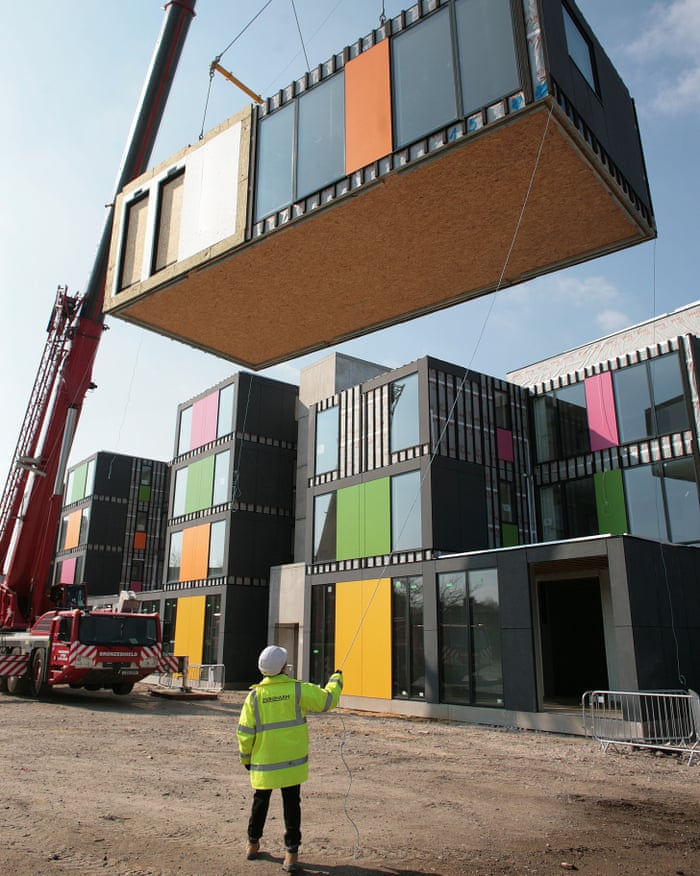
Quick, Combine-able Modular Housing
Cheaper and Longer Lasting Modular Homes
Bigger used to be better when it came to the housing market in America. Size still matters in the housing market but the scales are tipping in favor of the smaller end. There are many reasons for the reversal of housing preferences. Younger Americans are opting for a minimalist lifestyle that offers smaller and simpler living.
Many of the homeowners that are joining this movement are opting to live in tiny houses. These houses reduce the size of the home substantially but still offer many of the same amenities.
Americans are choosing to follow the tiny house movement for a variety of reasons. Among the top reasons are financial concerns, environmental concerns, and freedom from huge property maintenance. The typical American spends up to 50 percent of their income on normal housing costs. This cost can be reduced drastically by building a home to be just the size that you need.
A popular trend is to use the money saved on reducing the size to provide amazing amenities to the homes. There are tiny homes as small as 300 square feet that have solar power, hot tubs ad even bars. These could be purchased due to the amount of money saved by reducing square footage.
The trend of wanting smaller homes with high-quality materials and top of the line amenities is not only in the tiny house market but in the regular home market as well. Last year the typical new home that was manufactured dropped in square footage. This was the first drop in size since 2009 which shows that this trend is rapidly catching on.
The average millennial home buyer is looking for substance instead of size. House size is becoming less important. Many homeowners are looking for things like energy star rated appliances, smart thermostats, low energy windows, and other energy-efficient amenities. New homeowners also seem to be leaning toward patios, wrap around porches and separate laundry rooms.
Most people looking for a home prefer building a new structure as opposed to buying an existing home. This means that the homeowners can add the amenities and the square footage that they want as opposed to more expensive renovations to existing structures. These homeowners are also moving out of cities with 65% of them wanting to build their houses in the suburbs.
Most of these millennial first time homeowners would prefer to build a new house. However, most are purchasing existing homes simply because it is an easier process, they can get deals on foreclosed homes, and they can move in almost immediately.
These homeowners are turning to the reality television craze to learn how to add amenities and features to their homes on their own. These do it yourself home improvement shows are starting a trend of homeowners making improvements to their homes on their own.
Many of these renovations tend to be outdoor spaces for entertaining company and relaxing. Decks, fences, and vegetable gardens top the list but gazebos, swimming pools, hot tubs, and BBQ pits are up there on the top of the list as well.
The biggest thing these millennials are looking for is value. They are looking to add to the equity of these homes so they can flip them for a profit and build their own homes the way they want. After these homes sell, they are tending to build homes that are smaller and have amenities such as mud rooms, separate laundry rooms, and gathering places such as outdoor kitchens with a dining area. Millennials seem to like to gather in groups and be close-knit by having parties and cookouts.
The state of the economy forced many Americans to be frugal in spending. This is the reason the trend for building smaller homes began. New Home building companies are building smaller homes to stay in business. They knew that big extravagant homes were not going to sell in the market at the time and began to market smaller more affordable homes.
Over the last thirty years’ homes have more than doubled in size for the average home. Back then the average new home was 1,700 square feet. Any homeowner who has a house that was built in the previous decade has a living area that is four times larger than most of the homes built in the 1950’s. Many of these homes are being foreclosed and sold at low prices and in turn that brings down the price of other homes on the market.
Most construction companies are reporting that their clients are asking for smaller homes and 90% of these companies stated that they are either planning to build smaller homes or are already in the process of building them.
The trend to move toward smaller cost efficient homes began before or at the beginning of the recession. The housing market started to hit rock bottom and devastated homeowners began looking at these large homes as a bad investment and realized how much of a cash drain they had on their hands. These larger homes are not only more expensive because of the building materials but they cost more to heat and cool, property taxes are higher, and maintenance is harder and costs more.
Therefore, homeowners are transitioning to smaller homes. Smaller homes are more cost efficient, easier to clean, and cheaper to furnish with those high-quality amenities that everyone seems to want.
This trend can be seen in divorces of all things. Divorcing couples used to fight over who was going to get the house and all the costs associated with it because neither wanted it. Now divorcing couples are fighting to try and keep the homes for themselves.
Living in a smaller home also makes homeowners think wisely about the things they want in their home because of less space. All of this has led to homeowners using the money they saved to purchase the high-quality amenities.
These homeowners have made the decision to go with quality over quantity and everyone benefits from this trend. Not only is this trend great for the environment but also good for the housing market and economy because fewer people are foreclosing on homes because they can afford to keep them due to the money saved by swapping square footage for nice amenities.
Mankind has long sought ways to retain hot air in the winter and keep hot air out in the summer. In medieval days, workers would stuff walls with different materials such as straw and cover it with a mud plaster to keep air out. This method of stuffing walls with various materials to provide insulation was the go-to method until an accidental discovery was made in 1932.
In 1932 the process to make fiberglass was discovered and insulation in the form of blankets burst onto the scene. Although this created a huge stride in insulation, the process of making and installing the insulation was highly dangerous because of small glass particles being released into the air. This also posed a threat to occupants of the building being insulated.
These issues lead to the creation of spray foam which alleviated the dangers of the fiberglass and was also easier to install. However, spray insulation is not without its downside. Sprayed insulation is vulnerable to water which limits where it can be installed and any water getting to it ruins its insulative properties.
The newest innovation in insulation is thanks to a material called Aerogel created by NASA. Aerogel is a silica-based product that holds several Guinness Book of Records. Two of those records are lowest density solid and most importantly, the best insulator. Aerogel is made by taking silica alcogel and removing the water from it and replacing it with nothing but air. Aerogels can have a density as low as .001 grams per cubic centimeter and the reason they make such a fantastic insulator is because they eliminate convection, radiation, and conduction which are the three methods of heat transfer.
This aerogel technology lead to the invention of Thermablock. Thermablock comes in plastic incased strips that attach to studs of a wall that increase the overall R-Value by up to 35 percent regardless of cavity insulation. R-Value is the measurement that tells how well insulation keeps heat out in the summer and retains it in the winter. The higher the number the better the insulation. Thermablok can also be purchased with self-adhesive backing that makes it easy to install. Thermablok also contains the added benefits of never aging, mildewing, or molding. This is thanks to the hydrophobic properties of the aerogel. Thermablok is also environmentally safe and can be recycled because it is made up of amorphous silica.
When standard metal stud and gypsum board walls are tested with an infrared thermal test, the studs stand out glaringly obviously as the points of thermal conductivity. The biggest reason for energy loss in a building is thermal bridging. This is where Thermablok makes all the difference in the world. Since Thermablok utilizes aerogel which is composed of 95 percent air and is located between the stud and drywall, it breaks the thermal bridging connection and provides greater insulation.
Thermablock was tested by the US department of Energy’s Oak Ridge National Laboratory and J. M. Laboratory. The test compared two identical walls, one with Thermablok strips on each 2×4 stud, and the second wall without any Thermablok applied. The testing revealed that the wall with Thermablok strips improved the R-Value by almost 42 percent. Additional insulation was added to the wall cavity to stop thermal convection which added to the R-Value.
Thermablock has greatly increased energy savings in residential and commercial buildings which make it more cost efficient to heat a building in the winter and cool a building in the summer. We have come a long way since straw and mud and there is a little irony in the fact that the best current product to keep air out is comprised of 95% air.